Custom CNC Machining Services
We provides instant quotes for your custom CNC machined parts in different materials and finishes.Upload your design files and get started today!
- Tolerance down to 0.001 inches.
- 1 piece minimum
- Lead time as short as 3 day.
- Many Materials&Finishes to Choose
- Certificate:ISO13485,ISO9001,AS9100
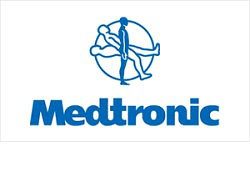
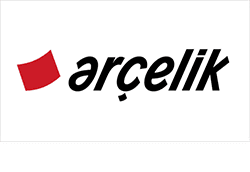
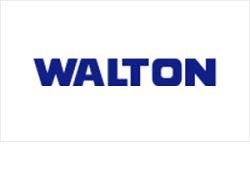
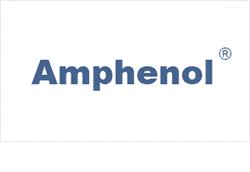
Our CNC Machining Advantages
FastenMetal owns a 3000 square meter CNC machining center and more than 500 CNC machines, 16 high-performance CNC machining equipment.Whether you require small batches or large-scale production, we’ve got you covered. With precise tolerance controls and extensive capabilities, we tailor our services to meet your volume needs while maintaining exceptional quality.
Custom CNC Milling Services
Our CNC milling center own over 200 CNC milling machines include 3-axis, 4-axis and advanced 5-axis CNC machines.We can machining special and challenging parts from a wide range of materials and finishes.
•Maximum stroke (3-axis machine): 1270×508×635 (mm).
•Maximum stroke (5-axis machine tool): 450×700×400 (mm), table rotation Φ400mm.
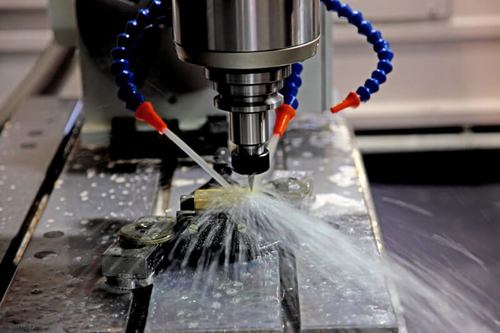
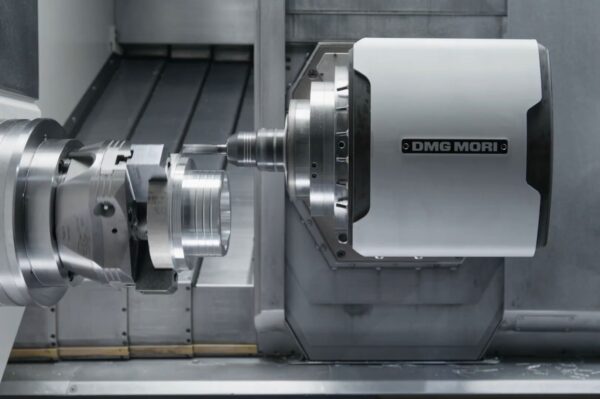
Custom CNC Turning Services
Our CNC center own advanced lathes produce cylindrical parts by rotating the workpiece while cutting tools shape it.
•Standard tolerances of ±0.01 mm; tighter tolerances down to ±0.005 mm can be achieved based on the material and complexity of the part.
• Maximun dimension typically up to 500 mm in diameter and 1500 mm in length.
Custom 5 axis machining Services
Our 5-axis CNC machining capabilities enable us to produce intricate geometries and seamless finishes in a single setup, reducing production time and ensuring consistency across every component.
•Maximum Part Size:4000×1500×600 mm
•General Tolerances:Within ±0.002 mm
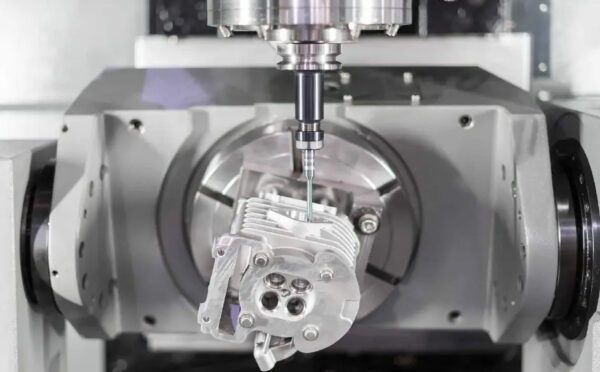
Part of Our Precise CNC Machining Display
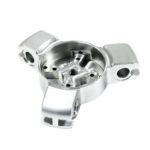
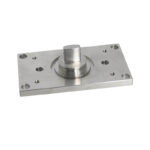
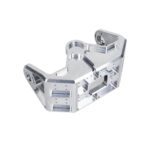
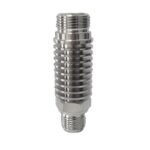
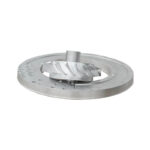
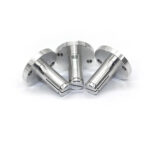
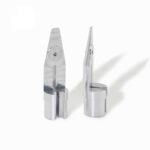
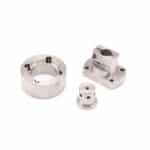
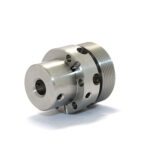
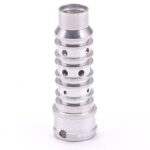
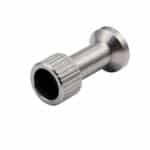
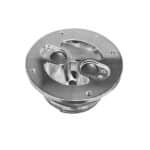
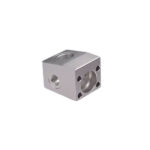
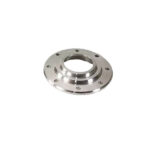
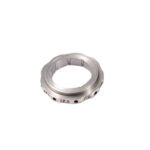
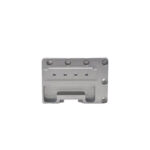
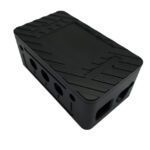
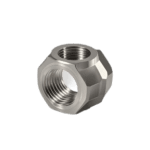
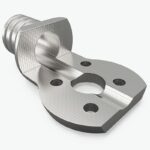
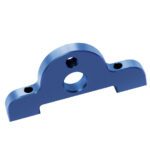
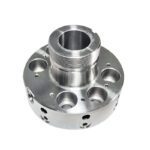
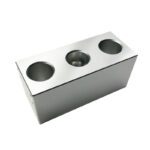
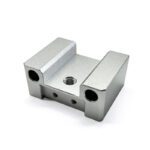
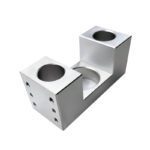
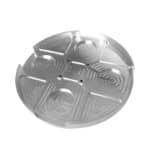
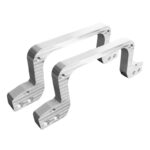
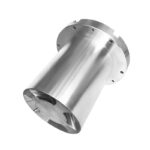
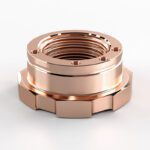
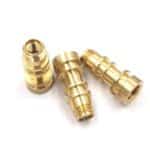
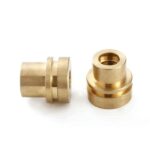
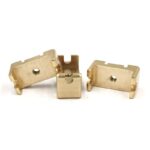
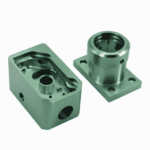
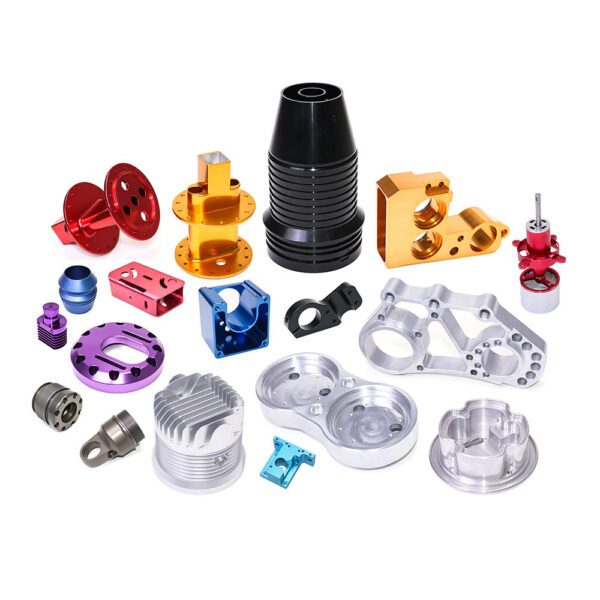
Aluminum CNC
Aluminum is a lightweight and high-strength material. The Aluminum materials we use for CNC machining is Aluminum 6061,2024,5052,5083,6061, etc.
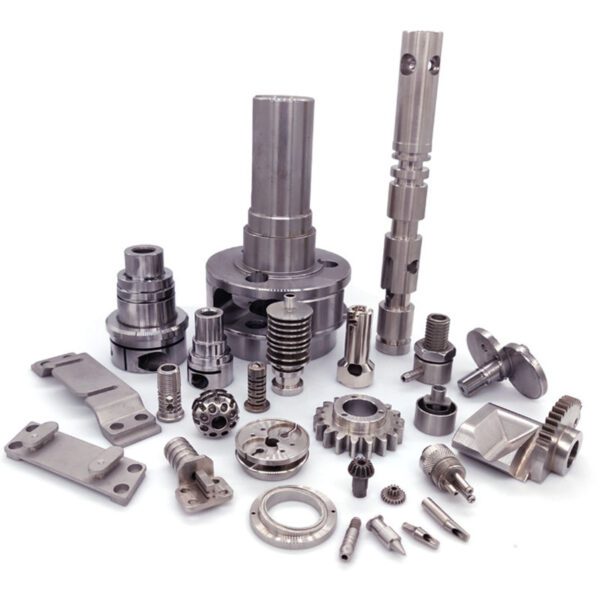
Stainless Steel CNC
We provide high quality and high strength stainless steel 304,316,430,etc for CNC machining.It is the most common material for CNC machining.
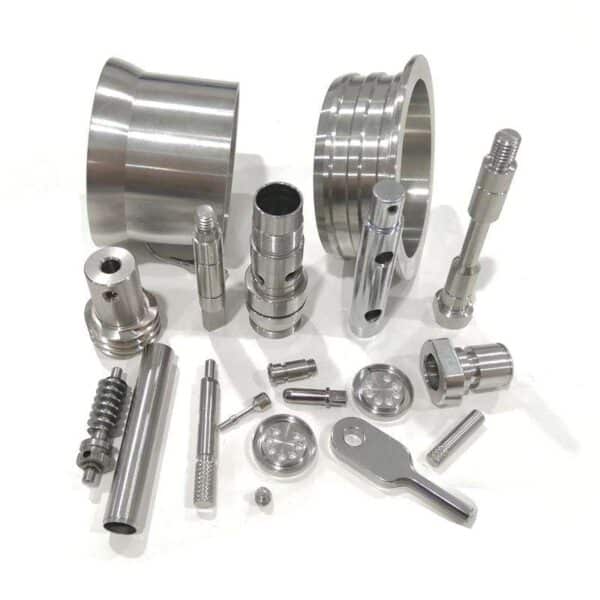
Titanium CNC
We provide high quality and high strength stainless steel 304,316,430,etc for CNC machining.It is the most common material for CNC machining.
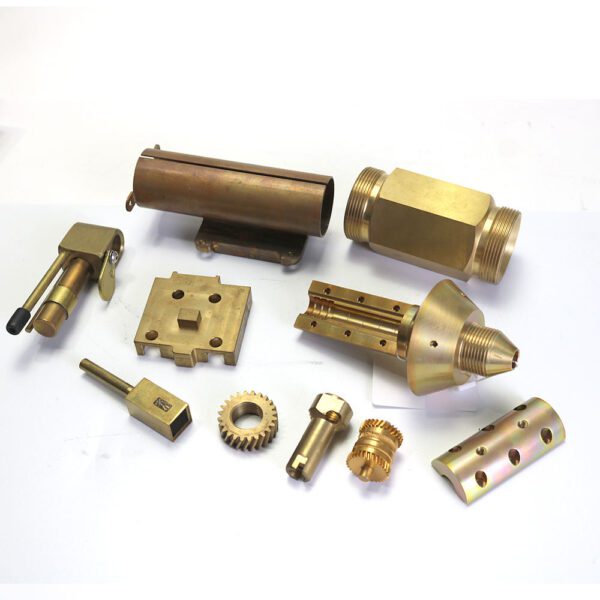
Brass CNC
We provide durable Brass materials C27400, C28000, C36000 for CNC Machining.The biggest brass parts we can machining is 200 cm x 80 cm x 100 cm
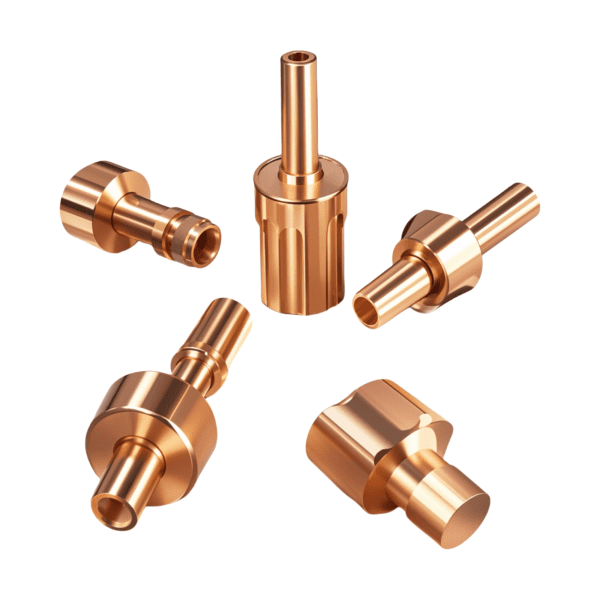
Copper CNC
The avaialble copper materials for CNC at FastenMetal include Copper C101(T2), C103(T1), C103(TU2), C110(TU0), Beryllium Copper, with tolerance down to±0.005″
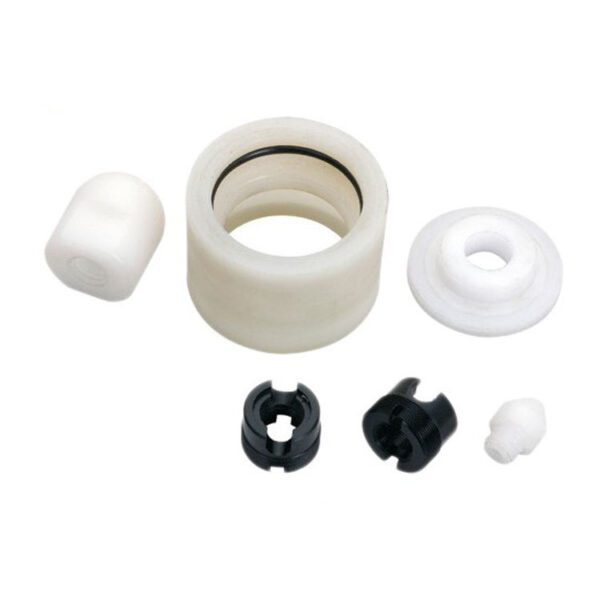
POM / ABS CNC
Parts machined by POM or ABS features igh stiffness, low friction, excellent dimensional stability, good wear resistance and easily machinable
How to Order CNC Machining Parts From Us?
1.Receive Design & Drawing
Our process begins with a thorough consultation to understand your project requirements. We evaluate the material specifications, including density, strength, and thermal properties, to ensure optimal performance. We also discuss finishes (e.g., anodizing, powder coating, or polishing), precision tolerances, and wall thickness to meet your application’s standards.
2.Receive Design & Drawing
Our process begins with a thorough consultation to understand your project requirements. We evaluate the material specifications, including density, strength, and thermal properties, to ensure optimal performance. We also discuss finishes (e.g., anodizing, powder coating, or polishing), precision tolerances, and wall thickness to meet your application’s standards.
3.Quotation
Once the design requirements are clear, we provide a detailed quotation. This includes material costs, machining time, surface finishing, and any additional services. Our transparent pricing ensures you understand every cost associated with your project.
4.Payment of Design Fee
Once the design requirements are clear, we To proceed with detailed design work, we require payment of a design fee. This fee covers the creation of CAD or 3D models, technical analysis, and prototyping preparation.
5.Make CAD or 3D Design
Using advanced CAD software, our design team creates detailed 2D and 3D models of your component. These models are shared with you for review and approval, ensuring all dimensions, tolerances, and features align with your specifications.
6.Make Sample, Approval by Customer
A prototype or sample is manufactured using our 5-axis CNC machining capabilities. This sample is meticulously inspected and tested for accuracy, functionality, and quality. Once the sample meets your standards, we seek your formal approval to proceed.
7.Confirmation on Order Detail
After sample approval, we confirm all order details, including quantities, delivery schedules, and any final adjustments to the design or specifications.
8.Signing Proforma Invoice (PI)
A proforma invoice (PI) is prepared, summarizing the order details, payment terms, and delivery timeline. Both parties sign the PI to formalize the agreement.
9.Receive Deposit
We require a deposit to initiate bulk production. The deposit amount is typically outlined in the PI and can vary based on the project scope.
10.Bulk Production
With the deposit received, we begin mass production. Our CNC machines ensure consistency and precision across every unit, adhering to the highest quality standards. Throughout the process, our quality control team conducts rigorous inspections at every stage.
11.Receive Balance
Before shipping the completed order, the balance payment is required. We provide detailed documentation, including quality inspection reports and photos of the finished products, for your peace of mind.
12.Delivery
Once the balance is received, we arrange for delivery. Depending on your preference, we can handle shipping via air, sea, or land. Our team ensures secure packaging to protect your components during transit, and we provide tracking information to keep you updated on your order’s status.
About Our CNC Machining Center
We are proud to operate a state-of-the-art CNC machining center spanning over 2,000 square meters, equipped with more than 500 advanced machines. Our capabilities include milling, turning, routing, EDM machining, drilling, and precision grinding, allowing us to handle a wide range of complicate and special parts.
We take products quality as most important. We maintain rigorous standards for surface finishes and cleanliness, ensuring that each part meets the highest level of precision and excellence. From polished and anodized finishes to powder coating and other custom options, we provide a wide variety of choices to suit your specific needs. Our comprehensive material selection and finishing options are designed to meet diverse application requirements, and our team is dedicated to providing expert support throughout your project. From initial design to final delivery, we ensure a seamless process and outstanding results. With an experienced team of engineers, we excel at crafting complex and unique parts with precision and reliability. Whether you require prototypes or large-scale production, our flexible capabilities allow us to handle both small and bulk orders efficiently, without compromising on quality or delivery timelines.
Partner with us for your CNC machining needs and experience superior craftsmanship, personalized service, and reliable results.
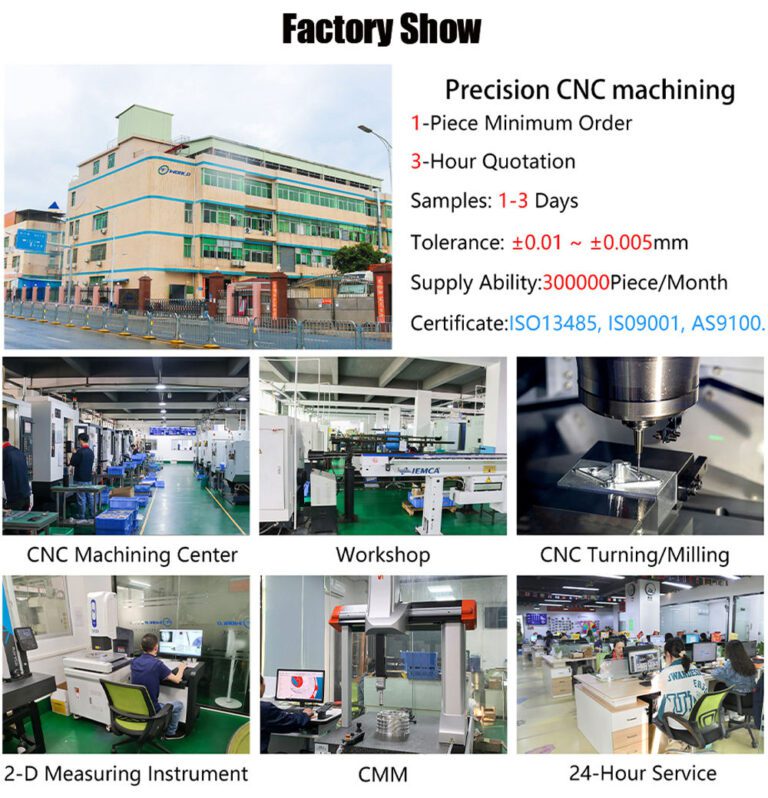
Precise of Our CNC Machining Parts
|
Metals with Drawing
|
Other Plastics with Drawing
|
---|---|---|
Linear Dimension
|
+/- 0.0025 mm +/- 0.0001 inch
|
+/- 0.05 mm
+/- 0.002 inch
|
Hole Diameters (Not Reamed)
|
+/- 0.0025 mm
+/- 0.0001 inch
|
+/- 0.05 mm
+/- 0.002 inch
|
Shaft Diameters
|
+/- 0.0025 mm
+/- 0.0001 inch
|
+/- 0.05 mm
+/- 0.002 inch
|
Maximum Part Size
|
Milling CNC: 4000×1500×600 mm
|
Turning CNC: 200×500 mm
|
Shipment
|
by sea, by air, by express, by post, etc.
|
/
|
Delivery Times
|
7-25 days depend on the order quality and products complication
|
/
|
Materials available for CNC Machining
Metal Materials
Aluminum is one of the most common and widely used materials in CNC machining, features its easily machining, lightweight, and light weight. Its unique characteristics make it an ideal choice for a wide range of industries, including aerospace, automotive, electronics, and medical.
Key advantages of aluminum in CNC machining:
High Machinability: Aluminum can be easily cut, shaped, and finished with precision, allowing for the production of intricate and complex components.
Corrosion Resistance: The natural oxide layer on aluminum provides excellent resistance to rust and corrosion, making it suitable for harsh environments.
Lightweight and Strong: Despite its low density, aluminum offers significant strength, making it a preferred material for applications where weight reduction is critical.
Thermal and Electrical Conductivity: Aluminum’s superior conductivity makes it an excellent choice for components requiring heat dissipation or electrical conductivity.
Cost-Effectiveness: Compared to other metals like titanium or stainless steel, aluminum is more affordable while still high performance.
Color: Silver
Types for Machining: 6061,6063, 7075, and 5052, each offering specific properties according to different applications.
Available Finishes:
- As-Machined (Raw Finish)
- Bead Blasting
- Anodizing
- Powder Coating
- Polishing
- Brushing
- Electroplating
- Chemical Conversion Coating (Alodine/Chromate Conversion)
- Painting
- Hard Anodizing
- Black Oxide Coating
- Passivation
Each finishing option offers unique benefits and is chosen based on the part’s functional requirements and aesthetic preferences.
Stainless steel is a popular material for CNC machining due to its strength, durability, and excellent corrosion resistance. It is widely used in industries like aerospace, automotive, medical, and food processing.
Color: Silver Grey
Stainless Steel Types available for Machining:
1.Austenitic Stainless Steels:Austenitic grades are the most widely used due to their excellent corrosion resistance and good mechanical properties. Include 304 (A2 Stainless Steel) and 316 (A4 Stainless Steel),303
2.Martensitic Stainless Steels:Martensitic grades are known for their hardness and strength but have lower corrosion resistance than austenitic steels. They are magnetic and can be heat-treated for additional strength.Include 410,420,440C
3.Ferritic Stainless Steels:Ferritic grades are magnetic and have moderate corrosion resistance. They are not as strong as martensitic or austenitic steels but are cost-effective for less demanding applications.Include 430,434
4.Duplex Stainless Steels:Duplex grades combine the benefits of austenitic and ferritic stainless steels, offering high strength and excellent corrosion resistance, particularly against stress corrosion cracking.Including 2205 and 2207(Super Duplex)
5.Precipitation-Hardening (PH) Stainless Steels:PH stainless steels are known for their high strength and corrosion resistance, achieved through a combination of heat treatment and precipitation hardening. Inlcuding 17-4 PH (630) and 15-5 PH
Finishes Available for Stainless Steel CNC Machining:
As-Machined Finish,Polishing,Brushing,Bead Blasting, Passivation, Electropolishing, Anodizing,Powder Coating,Black Oxide Coating
Carbon steel is a widely used material for CNC machining due to its strength, affordability, and versatility. carbon steel is available in various grades as per specific applications.
Carbon Steel Types available for Machining:
1.Low Carbon Steel (Mild Steel):
Low carbon steel contains up to 0.3% carbon, making it soft, ductile, and easy to machine.including:1018,1020,A36
2.Medium Carbon Steel
Medium carbon steel contains 0.3% to 0.6% carbon, offering a balance of strength, toughness, and wear resistance. It can be heat-treated for improved hardness and strength. Including 1045 and 1050
3.High Carbon Steel
High carbon steel contains 0.6% to 1.0% carbon, providing exceptional hardness and wear resistance. It is less ductile and more challenging to machine but excels in applications requiring durability. Including 1095,1080
4.Alloy Carbon Steel
Alloy carbon steels contain additional elements like chromium, nickel, or molybdenum to enhance properties such as strength, toughness, and corrosion resistance. Inlcuding 4140 (Chromoly Steel) and 4340
Finishes Available for Carbon Steel CNC Machining:
As finished, Painting, Powder Coating, Black Oxide Coating, Zinc Plating, Galvanizing, Oil Coating
Copper features its exceptional electrical and thermal conductivity, corrosion resistance, and malleability. It is widely used in industries like electronics, aerospace, and automotive for components such as electrical connectors, heat exchangers, and precision parts.
The common of copper for CNC machining we offer include pure copper (C110) for maximum conductivity, oxygen-free copper (C101) for enhanced purity, and tellurium copper (C145) for improved machinability. Copper alloys like brass, bronze, and beryllium copper offer additional strength, wear resistance, and ease of machining, making them suitable for diverse applications.
Finishes Available for Copper CNC Machining:As finished, Polishing, Brushing, Bead Blasting, Electroplating, Anodizing (For Copper Alloys), Powder Coating
Bronze features its excellent wear resistance, corrosion resistance, and machinability.As an alloy of copper and tin, often combined with other elements like aluminum or phosphorus, bronze offers high strength and low friction, making it ideal for applications such as bushings, bearings, gears, and marine components.
Finishes Available for Bronze CNC Machining:
As finished, Polishing, Brushing, Bead Blasting, Electroplating, Anodizing (For Copper Alloys), Powder Coating
Titanium is a premium material for CNC machining, known for its light weight,high strength corrosion resistance. It is widely used in industries such as aerospace, medical, and automotive for components requiring high performance under extreme conditions, such as implants, aircraft parts, and high-performance engine components.
Titanium Material Types Available for CNC Machining:
Titanium Alloy TA1 (Grade 1)
TA1 is a commercially pure titanium alloy with excellent corrosion resistance, high ductility, and low strength. It is lightweight, easy to form, and ideal for chemical processing, marine environments, and medical applications requiring biocompatibility.
Titanium Alloy TA2 (Grade 2):
TA2 is another commercially pure titanium alloy offering a balance of moderate strength, excellent corrosion resistance, and good weldability. It is commonly used in aerospace, marine, and industrial applications
Titanium Alloy TC4 (Ti-6Al-4V, Grade 5):
TC4 is a high-strength titanium alloy with light weigth, good corrosion resistance, and excellent machinability. Widely used in aerospace, medical implants, and high-performance automotive parts, TC4 is the most common titanium alloy.
Finishes Available for Titanium CNC Machining:
As finished, Polishing, Bead Blasting, Tumbling, Electropolish, Alodine, Anodizing, Electroless nickel, Painting, Powder coating, Brushed
Magnesium is a lightweight, strong,Corrosion Resistance,Good Thermal Conductivity material which often used in aerospace, automotive, and electronics industries.
Materials Available for Magnesium CNC Machining:
AZ Alloys (Aluminum-Zinc Alloys)
AZ31B: One of the most commonly used magnesium alloys, AZ31B contains aluminum and zinc, offering a good balance of strength, ductility, and corrosion resistance. It is often used in aerospace, automotive, and military applications.
AZ61A: Contains a higher percentage of zinc, offering improved strength and better high-temperature performance compared to AZ31B. It’s used in applications that require higher strength but may sacrifice some ductility.
AZ91D: A widely used magnesium alloy with higher zinc content, offering better strength and durability compared to AZ31B. It’s commonly used in die-casting and for parts in automotive and electronics.
Finishes Available for Magnesium CNC Machining:
Anodizing, Powder Coating,Chromate Conversion Coating
Plastics Materials
ABS is a strong and lightweight plastic commonly used in CNC machining. It is easy to machine, has good impact resistance, and offers excellent durability. ABS is ideal for making prototypes, housings, and mechanical parts due to its toughness and ability to handle wear and tear. It also has good chemical resistance and can be easily finished or painted
ABS types for CNC machining include Standard ABS,ABS-ESD,Flame-Retardant ABS,High-Impact ABS,Transparent ABS.
Finishes Available for ABS CNC Machining:
As Machined,Polished,Bead Blasting, Painting,Electroplating,Chemical Vapor Smoothing
POM, also known as Acetal or Delrin (a common brand name),it is a high-performance engineering thermoplastic widely used in CNC machining. It is prized for its excellent mechanical properties, machinability, and resistance to wear and chemicals.
Advantages of POM in CNC machining
1.Smooth surface finishes can be achieved with minimal post-processing.
2.Tolerances as tight as ±0.05 mm are possible.
3.Reduced tooling wear due to its machinability.
4.Cost-effective for producing both prototypes and small-to-medium production runs.
Finishes Available for POM CNC Machining
As Machined,Polished,Bead Blasting,Painting,Laser Marking,Coating
For more materials and finishes, please click here.
Types of Finishes Avaiable for Our CNC Machining Services
As finished
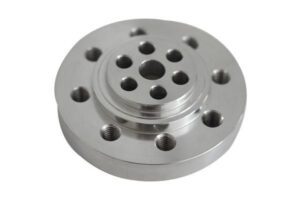
CNC parts are cleaned and deburred, leaving milling and tool marks visible. The default surface finish is Ra 125 microinches, with no extra treatments.
Anodized
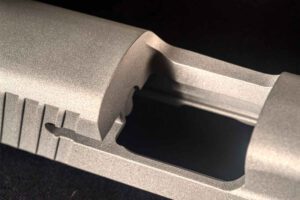
Anodizing is an electrochemical process that creates a clear, durable oxide layer on metal surfaces, improving corrosion resistance and appearance.
Bead Blasting
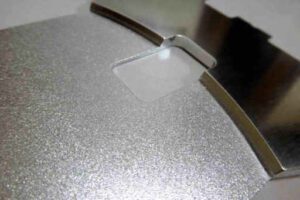
Bead blasting creates a smooth matte or satin finish by spraying the surface with fine abrasive particles, removing tool marks for a clean and attractive look.
Polishing
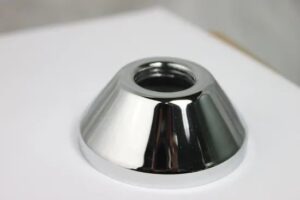
Polishing creates a smooth, shiny mirror finish on metal surfaces and can control material precisely, usually between 0.0001 and 0.0025 inches.
Powder Coating
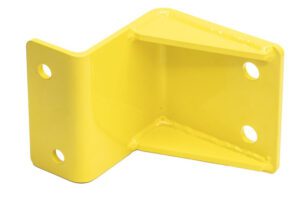
Powder coating applies a colored powder to the surface, then heats it to create a tough, protective layer with strong wear and corrosion resistance and a smooth finish.
Heat Treatment
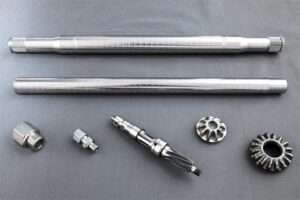
If not strict with a surface finish, heat treatments can alter the surface hardness and durability of the part, preparing it for demanding applications.
Brushing
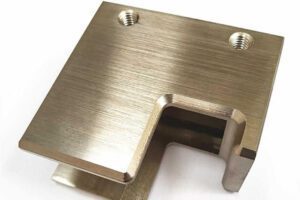
Brushing produces a uniform, linear texture on the surface, giving it a sleek and modern appearance. It is commonly used for decorative purposes.
Chem Film
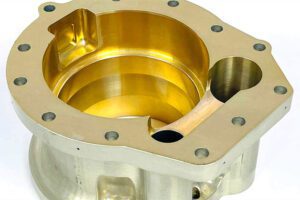
This process creates a thin, corrosion-resistant film on the metal surface without significantly altering its dimensions. It is often used for aluminum and magnesium parts.
For more materials and finishes, please click here.
Complete Numerical Control (NC) Machining Parameter Table
1. Machine Tool Basic Parameters
Parameter | Description | Typical Value/Range | Application Scenarios |
---|---|---|---|
X/Y/Z Axis Travel | Maximum movement range of each axis | 600×400×300 mm (standard) / ≥1000×800×500 mm (large-scale machines) | Workpiece size planning |
Spindle Speed | Rotations per minute (RPM) | 0–8,000 RPM (standard) / 10,000–50,000 RPM (high-speed precision machining) | High-speed aluminum cutting / Steel roughing |
Feed Rate | Tool movement speed | 50–5,000 mm/min (standard) / ≥10,000 mm/min (high-speed machining) | Adjust for material and precision |
Positioning Accuracy | Machine positioning error | ±0.005 mm (standard) / ±0.001 mm (high-precision machines) | Precision molds / Aerospace parts |
Repeat Positioning Accuracy | Positioning error after multiple operations | ±0.002 mm (standard) | Batch part machining |
2. Tool Parameters
Parameter | Description | Typical Value/Range | Application Scenarios |
---|---|---|---|
Tool Type | End mills, ball-nose cutters, drills, turning tools, etc. | – | Contouring / Drilling / Turning |
Tool Material | High-speed steel (HSS) / Carbide / Ceramic / Diamond | Carbide (steel) / Diamond (ultra-hard materials) | High-temperature alloys / Composites |
Tool Diameter | Cutting edge diameter | 0.1–20 mm (standard) / 0.01 mm (micro-machining) | Micro-hole drilling / Finishing |
Number of Flutes | Number of cutting edges | 2–6 flutes (multi-flute for finishing, fewer for chip evacuation) | Roughing vs. finishing transitions |
3. Cutting Parameters
Material | Cutting Speed (m/min) | Feed per Tooth (mm/tooth) | Cutting Depth (mm) |
---|---|---|---|
Aluminum | 200–1,000 | 0.1–0.3 (rough) / 0.01–0.1 (finish) | 2–5 (rough) / 0.1–1 (finish) |
Stainless Steel | 50–300 | 0.05–0.2 | 1–3 (rough) / 0.1–0.5 (finish) |
Titanium | 30–120 | 0.03–0.1 | 0.5–2 (rough) / 0.1–0.3 (finish) |
Carbon Steel | 80–200 | 0.1–0.4 | 2–4 (rough) / 0.2–0.8 (finish) |
4.Special Process Parameters
Process Type | Core Parameters | Typical Settings/Range |
High-Speed Machining (HSM) | Small depth of cut (0.1–0.5 mm) / High feed rate (≥10,000 mm/min) | Reduces tool load and improves surface finish
18
|
5-Axis Machining | Tool axis tilt angle (±30°) / Synchronization accuracy (≤0.005 mm) | Complex surface machining |
Micro-Machining | Spindle speed >50,000 RPM / Tool diameter <0.1 mm | Precision electronics / Medical devices |